Manufacturers should align with industrial software channel partners to facilitate migration to hybrid cloud platforms, that have end to end data integration, explains Kerry Grimes at AVEVA.
Since the 1990s, manufacturing organisations have taken gradual steps to automate and digitise their processes and operations by adopting ERP software. However, ERP applications were never intended to and remain challenged by not being able to effectively integrate and interpret the vast quantities of data produced by production equipment.
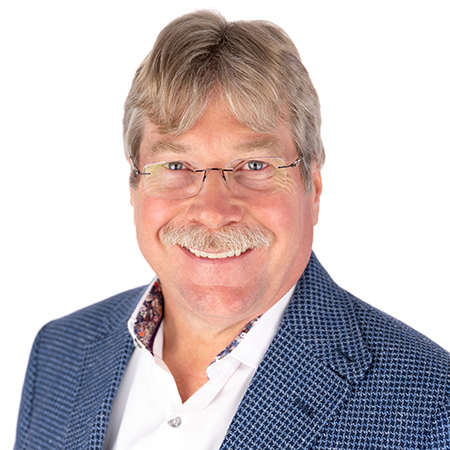
HMI, SCADA systems, manufacturing execution systems and other operational and control systems have been the standard for manufacturers on the plant floor. These existing systems, as well as ERP, are being challenged as industrial software is increasingly embracing digital platforms and being transformed into well integrated, end to end systems for the manufacturing sector.
Today’s incremental advances in big data, predictive analytics, business process management and augmented reality are enabling industrial manufacturing organisations to make sense of proprietary operational data like never before. What is more, digital platforms like cloud, Internet of Things, smart and edge devices are driving down the cost of digital transformation in the manufacturing sector.
Digital transformation is also driving a shift in how industrial software is consumed, moving from an on-premises, perpetual software ownership model as a capital expense into a periodic, subscription and cloud deployed model that can flexibly adapt to changing business requirements.
According to the World Economic Forum, the value of digital transformation in the Fourth Industrial Revolution is estimated at $100 trillion over the next ten years.
Manufacturing enterprises should enlist the services of industrial channel partners who are well skilled in cloud migration journeys and work closely with industrial software vendors who provide hybrid cloud, software subscriptions.
As machines become smarter through Industrial IoT, manufacturing execution systems are integrating machines with connected assets and transforming factories into seamless, smart organisations.
Inside the plant, visibility into operations and resources, aided by manufacturing execution systems, enables better decision making and collaboration between plant and enterprise functions. Historical production data provides insights into optimisation and continuous improvement.
However, unless manufacturing execution systems are able to digitally model the industrial manufacturing plant – by aligning with digital technologies and digital platforms – they will not be able to cope with the demands of transformation inside manufacturing plants.
According to the World Economic Forum, the value of digital transformation in the Fourth Industrial Revolution is estimated at $100 trillion over the next ten years, across all sectors, industries, and geographies. The manufacturing sector, which has long been a driver of global prosperity and economic growth, is key to this transformation.
Another transformational strand within manufacturing is the unification of storage and analytics, leveraging the domain expertise necessary to address industrial challenges, in a unified hybrid cloud solution that spans the entire value chain. Hybrid cloud platforms, operations control subscription solutions and industrial cloud software should not be viewed as separate entities, but rather as a single environment designed to address collaboration, scalability and security.
Again, selecting the right industrial channel partner – one that is well skilled in managing hybrid cloud based industrial software – is a vital step towards digital transformation for progressive manufacturing enterprises.
Selecting the right industrial channel partner, one that is well skilled in managing hybrid cloud based industrial software, is a vital step towards digital transformation.
Once the role of the manufacturing system has been aligned with digital platforms and digital technologies, the next step is the standardisation of enterprise-wide plant operations. This process governs operations and related information flow consistently across multiple manufacturing plants. Standardisation provides consistent visibility and engagement with all plant operations for improved business decisions and agility.
Standardisation is achieved through a reusable operations process modelling approach; an open engineering and runtime platform; and a broad suite of industrial applications scaling from plant performance optimisation to full manufacturing operations management functionality.
Hybrid cloud based, operations control subscription solutions help to boost standardisation by providing a digital thread from engineering to operations that uses performance intelligence to help industrial manufacturing enterprise build resilience and sustainability.
Having operations control software based on subscription models helps to eliminate traditional barriers to adoption by ensuring that end users can choose from a scalable set of solutions which are cybersecure, based on industry standards, and support full asset and operations lifecycle capabilities.
Typically, such a solution includes design, HMI-SCADA, supervisory control, analytics, AI-ML, AR-VR, asset performance, maintenance, and condition management, while only costing the services needed. This simplifies consumption of new capabilities, helping to accelerate the digital transformation journey.
Industrial channel companies, who have skills in digital technologies and platforms and deep manufacturing domain expertise, are the optimum partners to take up the role of trusted advisors for manufacturing enterprises.